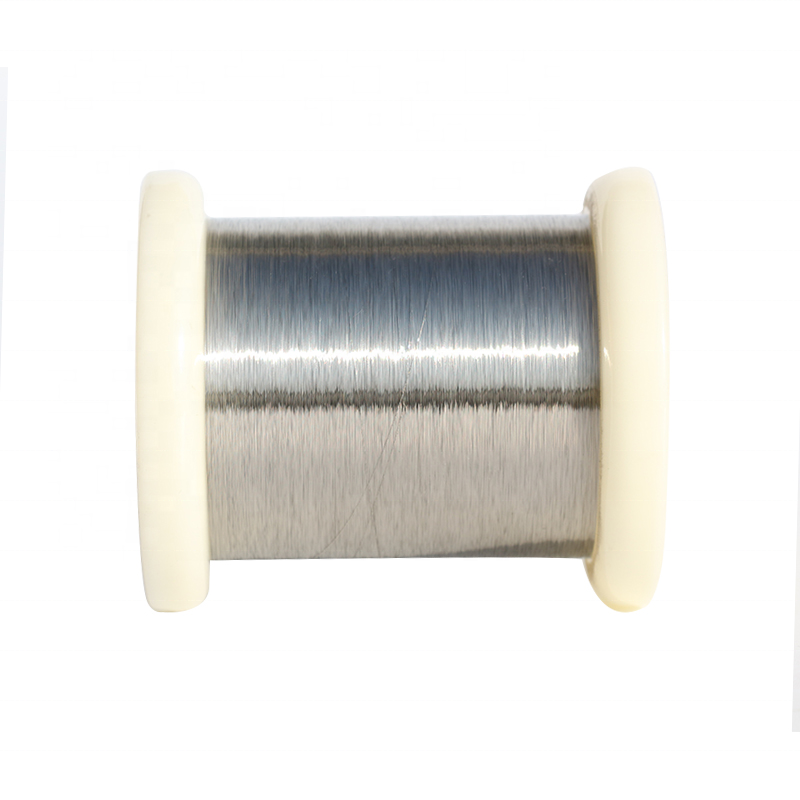
How is Copper-Nickel Wire Mesh Produced?
- Product Details
🏭 How is Copper-Nickel Wire Mesh Produced?
Copper-Nickel wire mesh is manufactured through a precise series of metallurgical and mechanical processes that transform raw copper-nickel alloy into fine, uniform woven mesh. The production process ensures dimensional accuracy, mechanical strength, and uniform conductivity, making it suitable for filtration, shielding, and marine applications.
🔧 Production Process Overview:
1. Alloy Melting and Casting
The process begins with melting high-purity copper and nickel to form the desired alloy, typically CuNi 70/30 or CuNi90/10.
Melting is done in an induction furnace to ensure uniform chemical composition.
The molten alloy is cast into billets or rods, which will be further processed into wire.
2. Hot Rolling / Extrusion
The cast billets are heated and hot-rolled or extruded into rods or wire bars.
This process reduces the diameter and improves the internal grain structure for better ductility.
3. Wire Drawing
The rods are drawn through a series of dies to gradually reduce the diameter to the required wire size.
This is typically done in multiple stages with intermediate annealing, to maintain flexibility and avoid cracking.
For fine meshes (e.g., 100 mesh and above), wires may be drawn to diameters as small as 0.05 mm (50 microns).
4. Annealing
After drawing, the wire is annealed in a controlled atmosphere furnace to soften it and remove internal stresses.
This improves the weavability and mechanical stability of the wire.
5. Weaving
The softened copper-nickel wire is woven using precision weaving looms into mesh structures.
Common weave types include:
Plain Weave (most common)
Twill Weave (for higher mesh counts or tighter structures)
The mesh size, wire diameter, and weave pattern are selected based on the final application, such as filtration, shielding, or reinforcement.
6. Surface Treatment and Cleaning
After weaving, the mesh is cleaned using ultrasonic cleaning or chemical degreasing to remove any oils, scale, or contaminants.
If needed, the mesh may also be annealed again to achieve desired softness or flexibility.
7. Inspection and Quality Control
The final mesh is tested for:
Mesh count and wire diameter consistency
Flatness and even tension
Electrical resistance and corrosion resistance
Surface defects or irregularities
8. Cutting, Slitting, or Rolling
The wire mesh is then:
Cut into sheets or slit into strips
Rolled into standard rolls (e.g., 10 m, 30 m, 50 m)
It is packaged securely to prevent damage or contamination during storage and transport.
📦 Summary of Production Flow:
Melting & Casting → Hot Rolling → Wire Drawing → Annealing → Weaving → Cleaning → QC → Cutting & Packaging
✅ Final Note:
At DLX ALLOY, we control each stage of the production process to deliver high-quality Copper-Nickel Wire Mesh with superior corrosion resistance, tight tolerances, and excellent conductivity — ready for demanding industrial and marine applications.
👉 Contact us for custom mesh sizes, detailed specifications, or free samples!