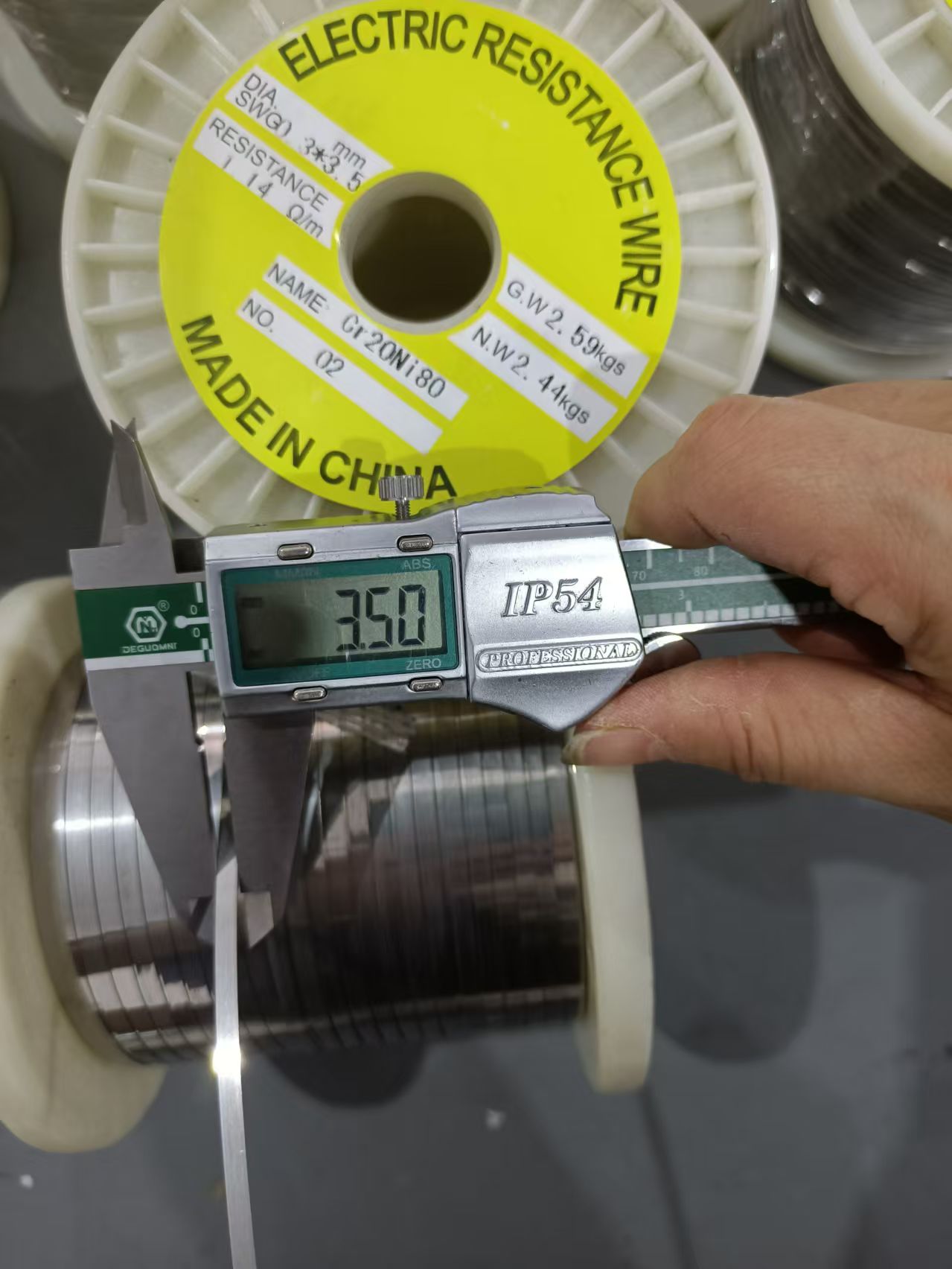
Ni80 Flat Wire for Heaters
- Product Details
Sure! Here's a professional and clear explanation of how Nichrome flat wire is produced, perfect for your website or customer education:
🏭 How is Nichrome Flat Wire Produced?
Nichrome flat wire — widely used in heating elements, resistors, and industrial furnaces — is manufactured through a careful series of melting, forming, and precision rolling processes.
The goal is to create a flat, uniform wire with excellent electrical resistance and mechanical strength.
📋 Main Production Steps:
1. Alloy Melting and Casting
Raw materials: Nickel (Ni) and Chromium (Cr) are mixed, sometimes with small amounts of Iron (Fe) or other elements depending on the specific Nichrome grade (like Ni80Cr20, Ni60Cr15, etc.).
Vacuum induction melting or air melting is used to produce a homogeneous molten alloy.
The molten Nichrome is then cast into large ingots.
2. Hot Rolling
The ingots are heated to a high temperature to make them soft and workable.
They undergo hot rolling, where the ingot is repeatedly compressed between rollers to reduce thickness and elongate into a thicker rod or sheet.
This process also refines the grain structure, improving mechanical properties.
3. Intermediate Annealing
After hot rolling, the material is annealed (heat-treated) to relieve internal stresses and improve ductility.
Annealing is crucial for preparing the material for cold working without cracking.
4. Cold Rolling to Strip
The semi-finished material is further cold rolled (at room temperature) into a thin strip.
Cold rolling improves surface quality, thickness precision, and mechanical strength.
The strip can be rolled down to various thicknesses depending on the final wire size requirement.
5. Edge Slitting (Optional)
If necessary, the wide strip is slit into narrower strips according to customer specifications.
6. Flat Wire Rolling/Forming
The strips are then rolled or drawn through specially designed flat wire rolling mills or turk’s head machines.
These machines control both thickness and width simultaneously to achieve a precisely dimensioned flat wire with very smooth surfaces and uniform properties.
7. Final Annealing (Soft State if Required)
Depending on the application, the finished flat wire may undergo a final annealing to soften it for easier winding or forming.
For heating elements that require some stiffness, a controlled hardness may be maintained.
8. Surface Cleaning and Inspection
The flat wire is cleaned (acid pickling, brushing, or ultrasonic cleaning) to remove oxides or rolling residues.
Then it is inspected for:
Dimensions (width, thickness, flatness)
Surface quality (no cracks, pits, or stains)
Electrical resistance uniformity
Mechanical properties (tensile strength, elongation)
9. Spooling and Packaging
The finished flat wire is wound onto plastic or metal spools, carefully tensioned to avoid deformation.
It is then packaged under controlled conditions to prevent contamination or oxidation before delivery.
✨ Summary:
Process Stage | Purpose |
---|---|
Melting & Casting | Produce uniform Nichrome alloy ingots |
Hot Rolling | Reduce ingot size and improve grain structure |
Annealing | Soften material for further processing |
Cold Rolling/Slitting | Achieve thin strips and exact dimensions |
Flat Wire Rolling | Form flat cross-section with high precision |
Cleaning & Inspection | Ensure quality, appearance, and performance |
Spooling & Packaging | Protect and prepare for shipping |
✅ Final Note:
At DLX ALLOY, we strictly control every step of the production of Nichrome flat wires to ensure tight tolerances, smooth surfaces, and consistent electrical resistance, meeting the demands of high-performance heating and industrial applications.
👉 Contact us today for custom sizes, technical support, or free samples!