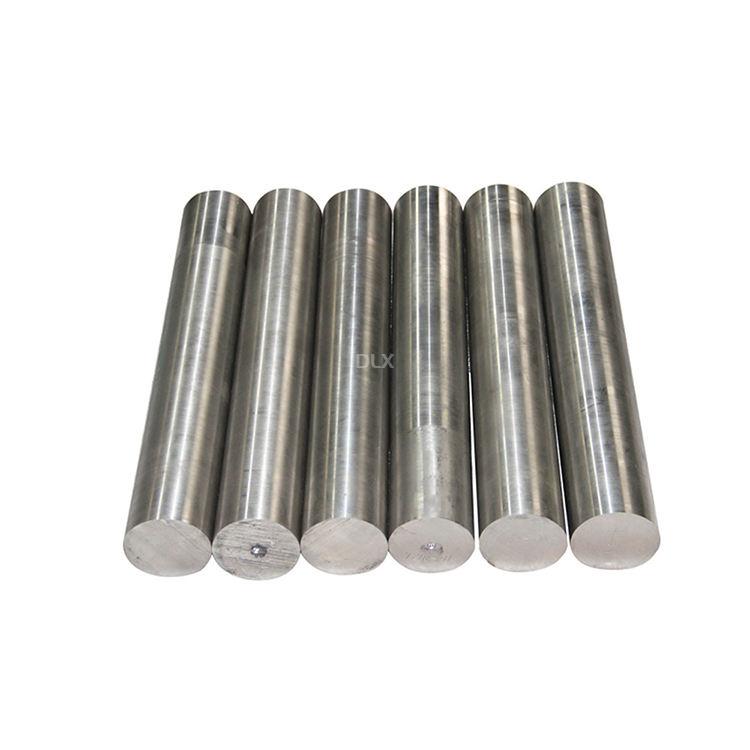
Cold Drawing Treatment Copper Bar And Copper Alloys with Ni-Cr Conductor Material
- Product Details
Our cold drawn copper bar and NiCr alloy conductor material are a dynamic duo for manufacturers who need top-tier conductivity and heat-resistant performance. Whether you’re building electrical systems or high-temperature heating components, these materials deliver the reliability and versatility to elevate your OEM projects.
Let’s start with the cold drawn copper bar. The cold drawing process works magic, boosting tensile strength to 300-400 MPa while keeping copper’s stellar electrical conductivity (~0.017 µΩ·m, one of the best out there). This makes it perfect for busbars, electrical connectors, and wiring where efficiency is key. The process also delivers a smooth, bright surface finish and precise dimensions, which saves time in manufacturing and ensures a polished look for high-end applications. While copper isn’t great in corrosive environments like seawater, its ductility and machinability make it a breeze to shape into custom components.
On the other hand, our NiCr alloy conductor material—typically 60-80% nickel and 15-20% chromium—is built for heat and durability. With a high resistivity of 1.0-1.5 µΩ·m and a low temperature coefficient of resistance (~100 ppm/°C), it’s a go-to for precision resistors and heating elements in toasters, ovens, and industrial furnaces. It thrives at temperatures up to 1200°C, forming a protective chromium oxide layer that fights off oxidation and corrosion in harsh, oxidizing environments (just avoid sulfur-heavy settings). Its tensile strength (600-800 MPa) and hardness (180-220 HV) ensure it holds up under stress, while its ductility allows for forming into wires, strips, or custom shapes.
The market for these materials is hot, with a growth rate of about 5-6% annually, driven by demand in electrical, aerospace, and industrial sectors. Cold drawn copper bars are essential for energy-efficient electrical systems, while NiCr alloys dominate in heating and aerospace applications like turbine components. Compared to CuNi44, copper offers unmatched conductivity for low-resistance needs, while NiCr excels in high-temperature stability.
We produce these materials with strict quality controls to ensure consistent performance—whether it’s the conductivity of our copper bars or the resistivity and heat resistance of our NiCr alloys. We’re also exploring sustainable practices, like recycling, to keep our process eco-friendly. While raw material prices can fluctuate, the durability and efficiency of these materials make them a cost-effective choice for long-term performance.
In short, our cold drawn copper bar and NiCr alloy conductor material are your ticket to high-performance manufacturing. From electrical systems to high-temperature heating, they deliver the conductivity, strength, and reliability you need to get the job done. Ready to power up your next project? These materials have you covered.
Product Description:
Our NiCr Alloy is made up of Copper Clad Steel, Inconel Nickel Alloy, and other high-quality materials. These materials are carefully selected to ensure that the final product meets our customer's expectations and requirements.
The melting point of our NiCr Alloy ranges from 1350-1400°C, making it an ideal choice for high temperature applications. It also has an elongation of 20-30%, which ensures that it can withstand stress without breaking or cracking.
Our NiCr Alloy is available for order with a leading time of 5~20 days, depending on the order quantity. We offer a free sample to our customers, so they can test the product's quality and performance before placing an order.
If you're looking for a reliable and durable NiCr Alloy, then look no further than our NCHW-1 model. Our product is designed to meet the needs of various industries such as aerospace, automotive, and manufacturing.
For more details, pls directly contact us.
Applications:
The melting range of DLX NiCr Alloy ranges from 1320-1370 °C, which makes it ideal for use in high-temperature applications such as furnace components, heating elements, and industrial furnaces. Its ability to resist oxidation and corrosion at high temperatures allows it to withstand harsh environments and remain durable over time.
The strand number of DLX NiCr Alloy ranges from 7, 19, 37, and more. This allows for a variety of applications and scenarios, including use in electrical heating systems, resistance wire, and for the manufacturing of thermocouples and other temperature sensors.
DLX NiCr Alloy comes in two states: soft and hard. The soft state is suitable for use in applications where ductility and flexibility are required, such as in wire mesh and other wire products. The hard state is suitable for use in applications where strength and durability are required, such as in springs and other mechanical components.
The treatment options available for DLX NiCr Alloy include annealed and cold drawing. Annealing is a heat treatment process that improves the ductility and toughness of the alloy, making it more suitable for use in wire products. Cold drawing is a process that increases the tensile strength and hardness of the alloy, making it more suitable for use in mechanical components such as springs and other parts.
DLX NiCr Alloy is exported from the port of Shanghai, China, and is widely used in various industries such as aerospace, automotive, and electronics. Its excellent resistance to oxidation and corrosion at high temperatures, combined with its ability to withstand harsh environments, make it an ideal choice for use in a wide range of applications.
Overall, DLX NiCr Alloy is a high-performance copper-based alloy that is widely used in various industries where high-temperature resistance, durability, and strength are required. Its versatility and range of applications make it an ideal choice for manufacturers and engineers looking for a reliable and durable material for their products.
Customization:
Our product customization services also extend to other materials such as Copper Based Alloys and Copper And Copper Alloys. Speak to our team today to learn more about our customization options and to place your order.
Support and Services:
NiCr Alloy is a high-performance material used in a variety of applications, including heating elements, furnace components, and electrical resistance wires. Our product technical support and services include:
Expert consultation on material selection and usage
Customized alloy design and development
Testing and analysis services to ensure product quality and performance
Technical documentation and training resources
Assistance with product installation, maintenance, and troubleshooting
Our team of experienced engineers and technicians are dedicated to providing superior technical support and services to our customers. Contact us today to learn more about our NiCr Alloy products and how we can assist you with your specific needs.
Packing and Shipping:
Product Packaging:
The NiCr Alloy product will be carefully packed in a sturdy cardboard box to ensure safe transportation.
The product will be wrapped in bubble wrap and placed in a plastic bag to prevent any scratches or damage during transit.
The box will be labeled with the product name and any necessary handling instructions.
Shipping:
The NiCr Alloy product will be shipped via a reputable carrier to ensure timely delivery.
Shipping options and costs will be calculated and presented to the customer at checkout.
The customer will receive a tracking number to monitor the status of their shipment.
In the event of any shipping issues, the customer can contact our customer service team for assistance.
About Us:
Our 12,000㎡ factory is equipped with complete capabilities for research, production, testing, and packaging. We strictly adhere to ISO 9001 standards in our production processes, with an annual output of 1,200 tons. This ensures that we meet both quantity and quality demands. Furthermore, all products undergo rigorous simulated environment testing including high temperature, high pressure, and corrosion tests before being dispatched, ensuring they meet customer specifications. We also provide chemical analysis reports for every FeCrAl alloy, NiCr alloy, and other products purchased.
For all our clients, we offer timely and multilingual after-sales support and technical consulting, helping you resolve any issues swiftly and efficiently.
Client Visits
Building Stronger Partnerships
We support all kinds of testing:
FAQs
What is a cold drawn copper bar?
It’s a copper bar processed through cold drawing, which enhances strength, improves surface finish, and maintains high electrical conductivity (~0.017 µΩ·m) for applications like busbars and conductors.
What is NiCr alloy conductor material?
NiCr (nickel-chromium) alloy, typically 60-80% nickel and 15-20% chromium, is a high-resistivity (~1.0-1.5 µΩ·m) conductor material used for heating elements and resistors due to its thermal stability.
What are their primary applications?
Cold drawn copper bars are used in electrical busbars, connectors, and wiring. NiCr alloys are used in heating elements (e.g., ovens, toasters), resistors, and thermocouples.
How does cold drawing benefit copper bars?
Cold drawing increases tensile strength (up to 300-400 MPa), improves dimensional precision, and enhances surface quality, making it ideal for high-performance electrical components.
How does NiCr alloy perform in corrosive environments?
NiCr alloys form a protective chromium oxide layer, offering excellent resistance to oxidation and corrosion in high-temperature, oxidizing environments (not sulfur-rich).
Can these materials handle high temperatures?
Copper bars are stable up to ~200°C, suitable for electrical applications. NiCr alloys withstand up to 1200°C, ideal for heating and furnace components.
Which industries use these materials?
Electrical, automotive, aerospace, and industrial manufacturing rely on copper for conductivity and NiCr for heating and resistance applications.
Are they easy to process for manufacturing?
Cold drawn copper is highly ductile and machinable. NiCr alloys are ductile and weldable but require care during machining due to hardness.
-
Corrosion-Resistant NiCr Alloy with High Thermal Conductivity and Precision Electrical Properties
Enquire Now -
Hot Sale OEM Melting Range From 1320°C To 1370 °C Nichrome Alloy Bar Material
Enquire Now -
New Hot Nickel Aluminum Bronze Bar Nickel Alloy B3 Round Bar/Rod For Sale
Enquire Now -
NiCr Alloy Bar NCHW-1 State Hard Trade Term EXW for Industrial Applications
Enquire Now