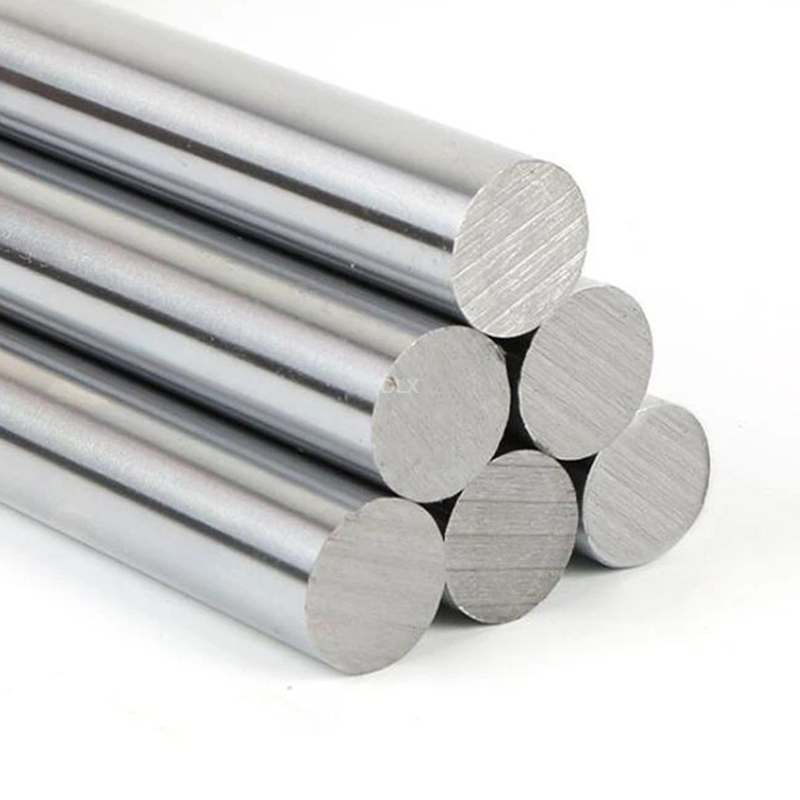
Melting Range of 1320-1370 °C Alloy Bar Material with 7 Strands
- Product Details
Our NiCr alloy bar, with a melting range of 1320-1370°C and a 7-strand configuration, is a hot pick for OEMs who need a material that combines high-temperature performance with flexibility and precision. Likely a nickel-chromium alloy (60-80% nickel, 15-20% chromium, like NiCr 80:20), this bar is engineered to shine in demanding applications where heat, corrosion, and electrical reliability are critical.
The 7-strand design is a standout feature, boosting flexibility and fatigue resistance compared to solid bars. This makes it perfect for applications like flexible heating elements or conductive components that need to bend without breaking, such as in aerospace wiring or industrial furnace coils. With a high resistivity of 1.0-1.5 µΩ·m and a low temperature coefficient of resistance (~100 ppm/°C), it’s a go-to for precision resistors, thermocouples, and heating elements in toasters, ovens, or heavy-duty furnaces. It’s stable up to 1200°C, thanks to a chromium oxide layer that fights off oxidation and corrosion in high-temperature, oxidizing environments (just avoid sulfur-heavy settings).
This alloy’s mechanical properties are just as impressive. With a tensile strength of 600-800 MPa, hardness of 180-220 HV, and 20-30% elongation, it’s tough yet ductile, making it easy to form into custom shapes or wires. The 7-strand structure adds extra durability under dynamic loads, while its weldability ensures seamless integration into OEM designs. Its thermal conductivity (11-17 W/m·K) supports efficient heat dissipation, keeping systems running smoothly.
The nickel-chromium alloy market is growing at a steady 5-6% annually, driven by demand in electrical, aerospace, and industrial sectors. With the rise of energy-efficient heating systems and high-performance electronics, this NiCr bar’s combination of flexibility, resistivity, and heat resistance makes it a top choice. Compared to FeCrAl alloys, it offers better ductility; compared to CuNi44, it handles higher temperatures, making it versatile for extreme conditions.
We produce this NiCr alloy bar with rigorous quality controls to ensure consistent resistivity, strength, and flexibility. The 7-strand configuration is crafted for optimal performance, and we’re equipped to customize it for your specific needs. We’re also exploring sustainable practices, like recycling nickel alloys, to keep our process eco-friendly. While raw material prices can fluctuate, the durability and low maintenance of this alloy make it a cost-effective investment.
In short, our NiCr alloy bar with a 1320-1370°C melting range and 7 strands is your go-to for high-performance applications. Whether you’re building heating elements, resistors, or flexible aerospace components, it delivers the heat resistance, flexibility, and precision you need to make your project a success.
Product Description:
The NiCr Alloy is available in two treatment options: annealed and cold drawing. Annealing is a heat treatment process that improves the ductility and toughness of the alloy while cold drawing increases its strength and hardness. The choice of treatment depends on the specific application and required properties of the alloy.
The melting range of the NiCr Alloy is between 1320-1370 °C, and it can be cast into various shapes such as rods, wires, and sheets. The alloy's high temperature resistance makes it ideal for use in applications where high temperature and corrosion resistance are required.
The NiCr Alloy is commonly used in the production of heating elements, furnaces, and industrial ovens. The high nickel content in the alloy gives it excellent resistance to oxidation and corrosion, making it suitable for use in harsh environments. The alloy's excellent mechanical properties, including high strength and ductility, make it ideal for use in the manufacture of components that must withstand high stress and pressure.
The NiCr Alloy is available on different trade terms, including FOB, EXW, and CIF, making it accessible to customers worldwide. Customers can choose the trade term that best suits their needs and budget.
In summary, the NiCr Alloy is a high temperature resistance alloy that is used in various industries where high temperature and corrosion resistance are required. It is available in different grades and treatment options and can be cast into various shapes. Its excellent mechanical and chemical properties make it ideal for use in the manufacture of components that must withstand harsh environments. With different trade terms, the NiCr Alloy is accessible to customers worldwide.
For more details, pls directly contact us.
Applications:
One of the most common applications of DLX NiCr Alloy is in the production of heating elements. The high melting range and excellent resistance to oxidation make it an ideal material for heating elements that operate at high temperatures. The product is also used in the manufacturing of electrical resistance wires, which are used in a variety of electrical applications.
Another important application of DLX NiCr Alloy is in the aerospace industry. The product is used in the production of aircraft engines and gas turbine components due to its high strength and resistance to corrosion. It is also commonly used in the manufacturing of heat exchangers, which are used in aircraft and spacecraft to regulate temperature.
DLX NiCr Alloy is also used in the automotive industry. It is used in the manufacturing of exhaust systems and catalytic converters due to its high-temperature resistance and corrosion resistance. The product is also used in the production of spark plug electrodes.
DLX NiCr Alloy is also used in the production of Aluminium Copper Alloy, Copper Alloy Plate, and Copper Clad Steel. The product is used as a coating material due to its resistance to corrosion and high-temperature resistance. It is also used in the manufacturing of electrodes and heating elements for welding applications.
In conclusion, DLX NiCr Alloy is a versatile product that has a wide range of applications in various industries. Its unique properties, such as high strength, resistance to corrosion, and high-temperature resistance, make it an ideal material for various applications. Whether it is used in the production of heating elements, aircraft engines, or automotive exhaust systems, DLX NiCr Alloy is sure to deliver excellent performance.
Customization:
DLX offers product customization services for NiCr Alloy, a type of alloy steel metal that contains nickel and chromium. This product is available in grade Ni60Cr23/Inconel601/UNS N06601/610H and can be traced back to its place of origin in China. The leading time for this product ranges from 5 to 20 days, depending on the order quantity. The nickel content of this product varies according to the material used. Its elongation rate ranges from 20-30%. Samples of this product are available for free.
DLX also specializes in copper and copper alloys, offering a wide range of customization options and high-quality products.
Support and Services:
Our NiCr Alloy product comes with comprehensive technical support and services to ensure optimal performance and longevity. Our team of experts is available to provide technical assistance and advice on the selection, installation, and maintenance of our NiCr Alloy products.
We also offer a range of services to support our customers, including product testing, inspection, and analysis. Our state-of-the-art facilities and equipment allow us to provide accurate and reliable testing results to help our customers optimize their production processes.
In addition, we offer training and education programs to help our customers improve their knowledge and skills in working with NiCr Alloy products. These programs cover a range of topics, including product handling, safety, and troubleshooting.
Overall, our commitment to providing exceptional technical support and services ensures that our customers can rely on our NiCr Alloy products for their critical applications.
Packing and Shipping:
Product packaging:
The NiCr Alloy product will be securely packaged in a sturdy cardboard box.
The product will be wrapped in bubble wrap to prevent any damage during shipping.
Each package will include a label with the product name, quantity, and any warnings or handling instructions.
Shipping:
Shipping will be handled by a reputable carrier, such as FedEx or UPS.
Orders will be processed and shipped within 1-2 business days of receipt.
Customers will receive a tracking number once their order has shipped, so they can track their package's progress.
Please note that shipping times may vary depending on the destination and carrier used.
About Us:
Our 12,000㎡ factory is equipped with complete capabilities for research, production, testing, and packaging. We strictly adhere to ISO 9001 standards in our production processes, with an annual output of 1,200 tons. This ensures that we meet both quantity and quality demands. Furthermore, all products undergo rigorous simulated environment testing including high temperature, high pressure, and corrosion tests before being dispatched, ensuring they meet customer specifications. We also provide chemical analysis reports for every FeCrAl alloy, NiCr alloy, and other products purchased.
For all our clients, we offer timely and multilingual after-sales support and technical consulting, helping you resolve any issues swiftly and efficiently.
Client Visits
Building Stronger Partnerships
We support all kinds of testing:
FAQs
What is the alloy bar material with a 1320-1370°C melting range and 7 strands?
It’s likely a nickel-chromium (NiCr) alloy, such as NiCr 80:20, with 60-80% nickel and 15-20% chromium, formed into a 7-strand bar, offering high resistivity (~1.0-1.5 µΩ·m) and thermal stability.
What does the 7-strand configuration mean?
The 7-strand design enhances flexibility and fatigue resistance, making it ideal for applications requiring bending or dynamic loads, such as heating elements or flexible conductors.
What are its primary applications?
It’s used in heating elements (e.g., industrial furnaces, toasters), precision resistors, thermocouples, and flexible conductive components in aerospace or electrical systems.
How does it perform in corrosive environments?
The alloy forms a protective chromium oxide layer, providing excellent resistance to oxidation and corrosion in high-temperature, oxidizing environments (avoid sulfur-rich conditions).
How does its resistivity compare to other alloys?
Its resistivity (~1.0-1.5 µΩ·m) is higher than CuNi44 (~0.49 µΩ·m) but similar to FeCrAl (~1.2-1.5 µΩ·m), making it ideal for heating and resistance applications.
Can it withstand high temperatures?
Yes, it’s stable up to 1200°C, with a melting range of 1320-1370°C, suitable for high-temperature applications like furnace elements and heating coils.
Which industries use this alloy bar?
Electrical, aerospace, automotive, and industrial manufacturing rely on it for heating elements, resistors, and flexible conductive components.
Is it easy to process for manufacturing?
The 7-strand configuration and good ductility make it easy to form, bend, and weld, ideal for custom OEM components, though machining requires care due to hardness.
-
Corrosion-Resistant NiCr Alloy with High Thermal Conductivity and Precision Electrical Properties
Enquire Now -
Hot Sale OEM Melting Range From 1320°C To 1370 °C Nichrome Alloy Bar Material
Enquire Now -
New Hot Nickel Aluminum Bronze Bar Nickel Alloy B3 Round Bar/Rod For Sale
Enquire Now -
Cold Drawing Treatment Copper Bar And Copper Alloys with Ni-Cr Conductor Material
Enquire Now